You might assume that making an electric car is much the same as making a car with a petrol or diesel engine. Simply take out said engine and fuel tank and replace them with an electric motor (or two) and a battery pack. While there's some truth to that, the EV production process is undergoing rapid transformation.
Some car makers — Volvo and BMW particularly — build electric and combustion-engine cars on the same production line in the same factory.
However, the electric car is changing the way the motor industry builds cars, and it’s evolving fast. The fastest change of all has been in the world of batteries. Read on as we explore how electric cars are made...
How Are Electric Car Batteries Made?
Now, the norm is rapidly heading towards 100kWh batteries and ranges of more than 700, even 750km. The batteries of the latest electric cars are fundamentally the same in terms of their chemistry as those original Leaf batteries — they use the same lithium-ion construction as the battery in your phone or laptop — but they’re more robust, longer lasting, and far more technologically advanced in the way they’re managed by the car’s on-board electronics.
Batteries are also now being built closer to where the cars themselves are made. Back in 2012, batteries were generally made by a battery-making company (Panasonic and LG Chem among the biggies) and shipped to the car factory like any other component. Now, the trend is to co-locate battery-making plants with car factories, and car companies are increasingly taking control of the battery-making process.
The EV Production Process: How Electric Cars Are Manufactured
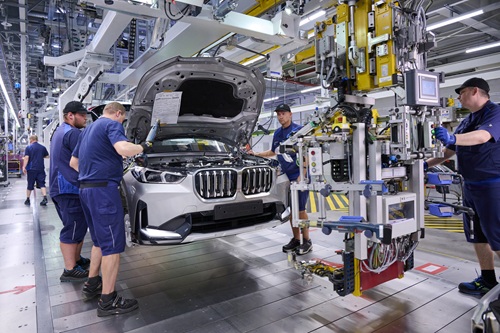
All of that has fundamental effects on how cars are made. Take BMW for example — its ‘home’ factory in Munich has been making four-and-six-cylinder engined cars since the 1950s, but now it’s all change as the company gears up to produce it’s all-important ‘Neue Klasse’ saloon, which will become the all-electric BMW 3 Series in 2027. “With the Neue Klasse, we will significantly reduce manufacturing costs at the Munich Plant,” says Plant Director Peter Weber. “In addition to optimised production processes and targeted automation, the Neue Klasse’s new vehicle architecture will also leverage further efficiencies. Focusing on a single drive train variant reduces production steps and the number of parts – for example, for wiring harnesses, which previously varied according to engine type and can be complex to install.” All these things add up and change how electric cars are made.
So, car production should become more efficient and simpler, and that should help to bring the prices of electric cars — already tumbling fast — down even further. The developments in battery technology should help too. Looking again at BMW, the company expects the sixth-generation batteries that it’s designed for the Neue Klasse to be cheaper to build, more efficient, and give the car around 30 per cent more range than a contemporary EV.
Carbon impact
A critical change to the way cars, and especially electric cars, are being made is in the power used by the factories. There has been much talk of late about electric cars needing huge amounts of energy to build, and that’s true — it’s why some estimates have it that you need to drive a new EV more more than 50,000km before its zero-emissions driving starts to pay back the energy cost of making it in the first place.
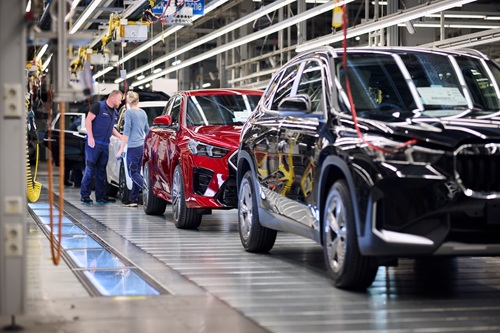
However, that figure can be altered, radically, if the energy used by the factory is fully renewable. This is Volkswagen’s plan, to make its EVs in carbon-neutral factories so that when they hit the dealer forecourt, there’s no carbon debt to be paid back. That process can be further helped by making sure that as much renewable energy as possible is being pumped into national grids, so that EVs can be charged-up with carbon-neutral power. It’s why VW is supporting the development not just of electric cars, but the solar and wind farms to charge them: “We plan to step up our commitment in the field of renewable energies each year in line with the development in sales of ID. models,” says Andreas Walingen, CSO and Head of Strategy of the Volkswagen Passenger Cars brand. “Through the large-scale development of European wind and solar farms, we intend to support our customers in the region in their efforts to always use their ID. vehicles in a net carbon-neutral way. This shows that our commitment to sustainability goes far beyond the electrification of vehicles.”
The Future of EV Production: Gigacasting and Advanced Manufacturing
Electric cars are also radically changing the very structure of our cars. Car makers around the world are starting to talk about giga-castings.
As with any buzz-phrase, there’s a whole plethora of actual, technical meanings to this, but in its essentials, gigacasting means making cars with fewer bits, making for cars that are much more affordable and efficient to build. That leads not only to potentially more affordable electric models, but also cars that don’t need as much energy in their construction phase, dramatically cutting their carbon footprint.
To do that, Toyota — for one — has developed a new way of building the basic structure of its cars. As reported by Nikkei, the company has developed a new so-called ‘Gigapress’ which cuts the number of individual parts and processes and utterly changes how electric cars are made.
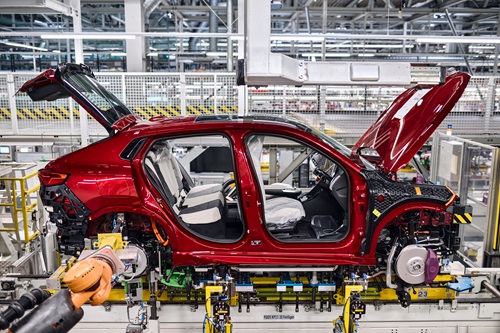
Currently, a car’s ‘platform’ (basically the lower structure, the suspension pickup points, and firewalls) is made up of hundreds of individual parts and stampings, all of which have to be welded together like a complex metallic 3D jigsaw. The new Gigapress does away with that, and instead pours molten aluminium into a mould which, when set, forms the front, rear, or centre structure of the car. The individual sections can then be adjusted for size depending on which car you’re making at which factory on what day.
In existing processes, according to Toyota, making one of these sections uses around 86 parts, 33 separate production processes, and takes many hours. The new Gigapress apparently can do the same job in about three minutes.
It’s part of a plan to entirely change the way the inside of a car factory works. Toyota plans to almost do away with the current system of conveyors and hoists, which slowly shuffle cars along as they are made. Instead, electric cars can actually roll under their own power, or be attached to autonomous towing rigs, allowing for a more efficient use of factory space.
So the structures of our cars are changing at a fundamental level, but so too are the batteries. Toyota claims that it has finally cracked the knack of making solid-state batteries for cars, and it intends to have the technology on sale soon.
Solid-State Batteries: The Future of EV Battery Production
A solid-state battery, using a ceramic-style electrolyte is far safer, far more rugged, and can in theory be fully charged in minutes, not hours. In laboratory bench tests, solid-state batteries can be fully charged in around 15 minutes, a figure that would be a major game-changer in electric car terms.
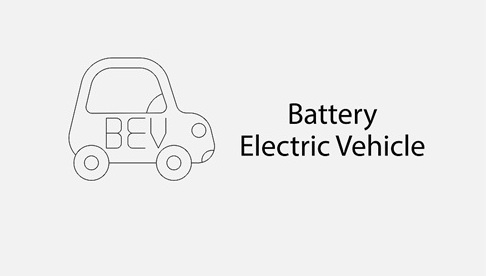
Toyota’s senior battery engineer, Keiji Kaita, has said that the prototype batteries on which the company has been working charge in just that amount of time, but he didn’t elaborate on what kind of power capacity the batteries have. Clearly, though, with such short recharging times, an EV with a solid-state battery would be able to do without a big, heavy, long-range battery because it could be topped up so much more easily.
At first, cars using solid-state batteries will be very expensive, though. It’s possible that, as with the original Prius and the first-generation Mirai hydrogen car, we could see Toyota subsidise the prices of such cars, accepting a loss-leader status in order to get the technology out on the road, much as it did with the first-generation Prius in the late 1990s.
Currently, the batteries have to be built in an “ultra-dry, nonaqueous environment” by specialists wearing protective gear, a situation Toyota has described as “less than ideal” and not conducive to mass-production. On the upside the batteries are said to have impressive performance, and Toyota claims that they can remain up to 90 per cent efficient for as long as 30 years.
Right now, electric cars mostly look just like any other car. That’s going to change radically in the coming years, though. The evolution has just begun.